- By Admin
- 2025/4/8 15:58:00
PET preform mold manufacturing process
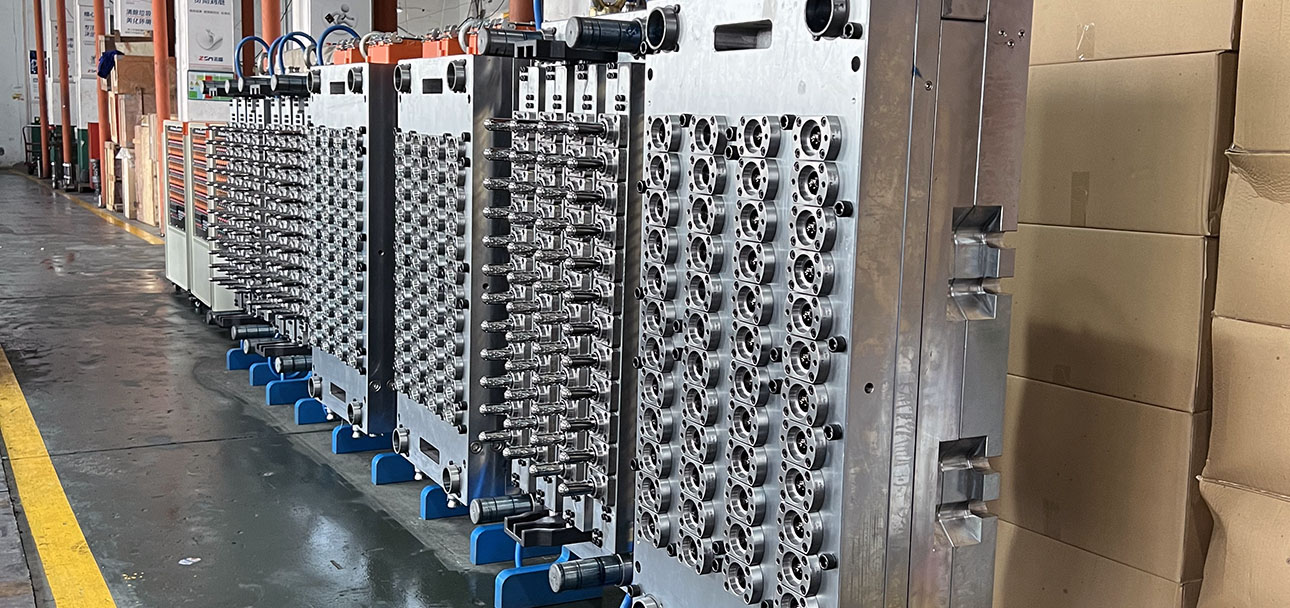
The manufacturing process of PET preform molds involves several precise steps to ensure high-quality molds capable of producing uniform and defect-free preforms for blow molding bottles. Below is a detailed breakdown of the process:
1. Design & Engineering
-
3D Modeling: The mold design is created using CAD software (e.g., SolidWorks, AutoCAD) based on preform specifications (weight, neck finish, wall thickness, etc.).
-
Simulation Analysis: Software like Moldflow simulates injection molding to predict flow, cooling, and potential defects.
-
Core & Cavity Design: The mold consists of:
-
Cavity (Female Part): Forms the outer shape of the preform.
-
Core (Male Part): Shapes the inner wall and neck finish.
-
Neck Ring: Ensures precise threading and sealing surface.
-
2. Material Selection
-
Mold Base: Typically made from hardened steel (e.g., P20, H13, S136) for durability.
-
Cavity & Core: High-grade stainless steel or tool steel (e.g., 420SS, NAK80) for corrosion resistance and polishability.
-
Cooling Channels: Copper or beryllium alloys for efficient heat transfer.
3. CNC Machining
-
Rough Machining: Blocks of steel are milled to approximate shapes.
-
Precision Machining: CNC milling, EDM (Electrical Discharge Machining), or wire cutting refines critical surfaces (neck finish, inner walls).
-
High-Speed Machining: For fine details like thread profiles.
4. Heat Treatment & Hardening
-
Hardening: Steel components are heat-treated (e.g., vacuum hardening) to achieve HRC 48–52 for wear resistance.
-
Tempering: Reduces brittleness post-hardening.
5. Surface Finishing
-
Polishing: Mirror-like finish (Ra < 0.05 µm) to prevent preform sticking and ensure smooth ejection.
-
Texture Application: For special finishes (e.g., matte or glossy preforms).
6. Assembly & Fitting
-
Cooling System: Channels are drilled for water circulation to control mold temperature.
-
Ejection System: Pins and sleeves are installed for preform ejection.
-
Alignment: Guide pins and bushings ensure precise core-cavity alignment.
7. Testing & Validation
-
Trial Molding: Test runs with PET material to check:
-
Dimensional accuracy (neck inner diameter, wall thickness).
-
Cooling efficiency (to prevent crystallinity or warping).
-
Ejection reliability.
-
-
Adjustments: Fine-tuning cooling rates, gate size, or venting if defects (e.g., splay, sink marks) occur.
8. Production & Maintenance
-
Mass Production: Mold is mounted in an injection molding machine for high-volume preform manufacturing.
-
Maintenance: Regular cleaning, lubrication, and inspection to prevent wear or corrosion.
Key Quality Considerations
-
Precision Tolerance: ±0.005 mm for critical areas (neck finish).
-
Cooling Uniformity: Avoids uneven shrinkage or stress in preforms.
-
Venting: Prevents air traps that cause burns or incomplete fills.
Advanced Techniques
-
Conformal Cooling: 3D-printed cooling channels for faster cycle times.
-
Multi-Cavity Molds: 48–144 cavities for high-output production.
This process ensures PET preform molds meet stringent requirements for clarity, strength, and consistency in bottle manufacturing. Let me know if you'd like details on a specific step!